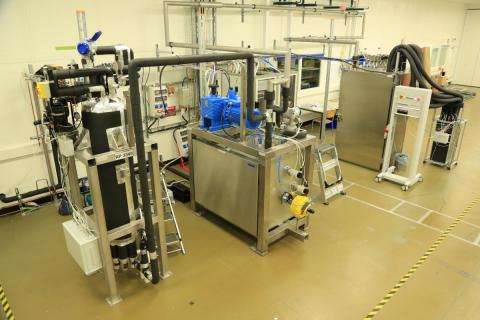
Paola Tropea
The cooling team of EP-DT has been mandated for the design, construction and commissioning of a full-scale prototype CO2 plant for the CMS Tracker Integration Facility (TIF) facility and the plant for the new Pixel system. The full-scale prototype is the largest plant (15 kW) ever built using a CO2 pumped two-phase principle.
An integrated approach has been adopted during the design phase, putting together a team of EP-DT and CMX experts. Intensive work has been put in selecting the most appropriate components, respecting the technical specification of 110 bar service pressure and a -40 oC operation temperature, which guarantees a large margin with respect to the design detector evaporating temperature of -20 oC. For the manifold components, additional requirements are radiation resistance and magnetic field tolerance, since the final manifold of the CMS Pixel CO2 cooling system will sit in the experimental cavern.
The EP-DT Gas team, responsible for the construction and M&O of detector’s gas systems since many years, has been in charge for the construction of the cooling plant. Substantial effort has been put on the quality control of the production, with visual and x-ray inspection of welds and fine tuning of the welding procedures up to the final version, according to the standards required by the European Pressure Equipment Directive.
Once installed at the TIF, the cooling plant and the manifold have been connected by means of co-axial transfer lines, where the liquid feeding the manifold runs in the inlet pipe, whilst the gas and liquid mixture returning to the plant continues its evaporation in the outlet pipe, maintaining the liquid line in sub-cooled state. The two pipes have been insulated by means of a vacuum jacket.
The process control systems have been developed thanks to the joint effort of the EP-DT gas and cooling crews. The general layout implemented, common to gas systems and other CO2 cooling systems designed in the EP-DT group, is based on a Schneider Programmable Logic Controller (PLC) for the process control, and a user interface based on WinCC OA SCADA system. The control software conforms to the UNICOS CPC6 (Unified Industrial Control System Continuous Process Control) framework of CERN.
The commissioning process at TIF has started with the electrical and control connections checkout, followed by the validation of system sub-assemblies: the accumulator, the pump, etc. The operation covers low and high flows and temperatures, allowing a careful margin for further request of the detector, connecting the plant to an ad-hoc dummy load: this has improved the overall performance and pushed the single components to their operation limits, acknowledging for the discovery of a few non-conformities on some of them. In addition, the transfer lines between the cooling plant and the manifold have been tested in operation and their design has been validated for the installation in the CMS underground premises with the final plant and manifolds.
Today, the cooling system's general layout has been validated, as well as 95% of the components. The fine-tuning of the TIF cooling system will continue in the next months, up to the connection of the first detector full-scale mock-up.